The Future of Lithium Batteries in the Electric Vehicle (EV) Industry
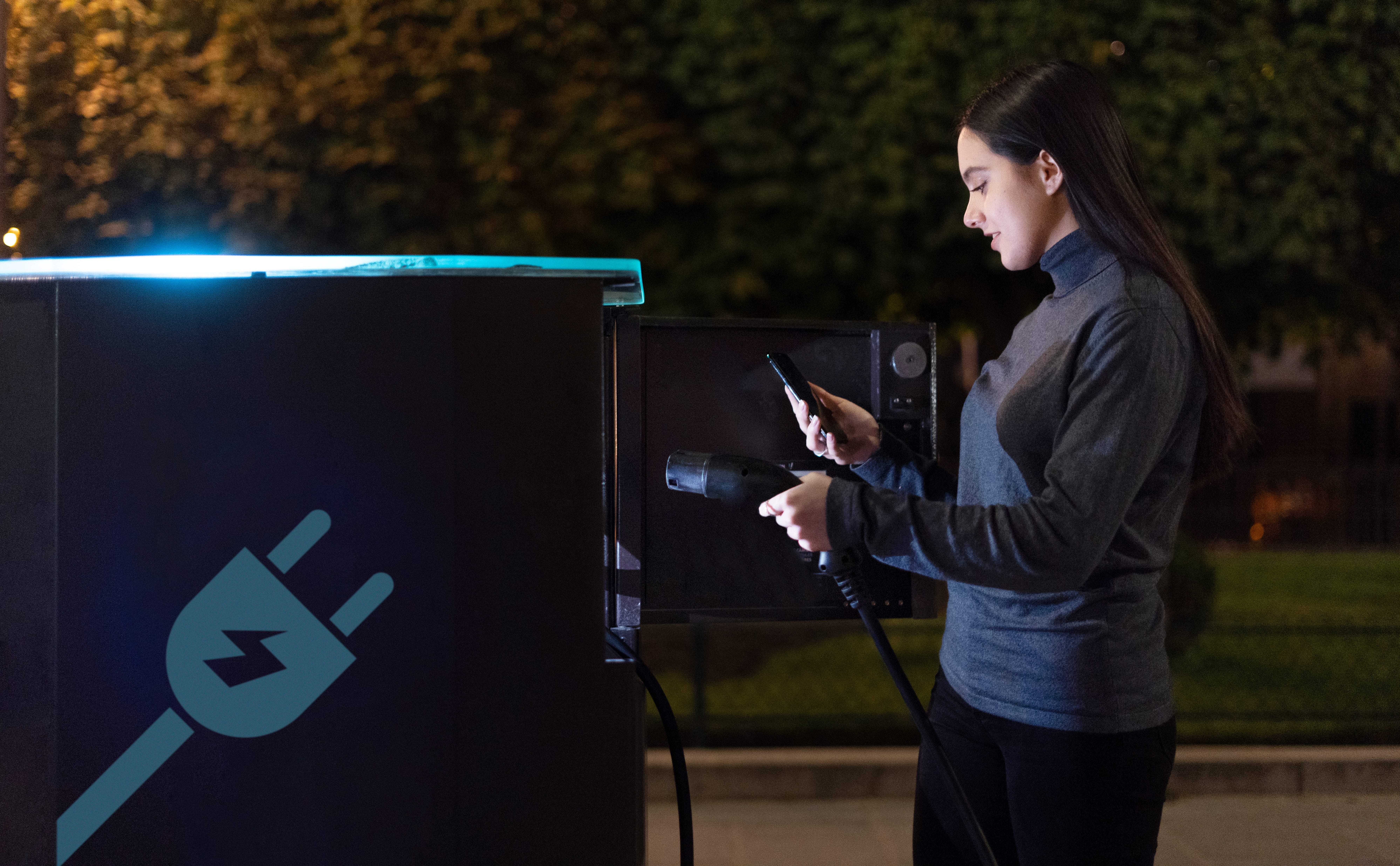
Electric Vehicles (EVs) have shifted from being a luxury option to becoming a mainstream choice in recent years. Central to the EV revolution is the lithium-ion battery, which has powered the journey from early electric models to today’s high-performance vehicles. As the industry continues to grow, the future of lithium batteries is a major area of focus, with advancements in battery technology set to revolutionise range, charging speed, sustainability, and safety. This blog explores the exciting possibilities, challenges, and key innovations on the horizon for lithium batteries in the EV industry.
Evolution of Lithium Batteries for EVs
Initially developed in the 1970s, lithium-ion batteries were commercialized in the early 1990s and soon became a staple in the consumer electronics market. The transition to EVs in the 21st century required a step-change in performance, with a demand for higher energy densities, longer lifespans, and faster charging.
The next frontier for lithium batteries in EVs focuses on maximizing energy density, improving longevity, enhancing safety, and reducing charging times. These goals are guiding innovations in materials, cell design, and manufacturing methods.
Key Innovations in Lithium Battery Technology
The drive to improve lithium batteries has led to a variety of technological innovations, some of which are already influencing the EV market, while others are still in development.
Lithium Iron Phosphate (LFP) Batteries
LFP batteries are gaining traction due to their stability, cost-effectiveness, and longer cycle life. They offer a safer alternative to traditional lithium-ion batteries, especially in high-temperature conditions, reducing the risk of overheating and combustion. Although they have lower energy density, LFP batteries are becoming popular in economy EV models, thanks to their affordability and durability.
Solid-State Batteries
Solid-state batteries replace the liquid electrolyte in conventional lithium-ion batteries with a solid material, which improves safety and enables higher energy densities. They are expected to double the range of today’s EVs while significantly reducing charging time. Companies like Toyota and QuantumScape are making strides in this area, with commercialization anticipated within the next decade.
Silicon Anode Technology
Traditional lithium-ion batteries use graphite as the anode, but silicon can store up to ten times more lithium, increasing the battery’s energy density and potentially extending EV range. However, silicon expands and contracts during charging cycles, leading to degradation. Researchers are developing advanced silicon anode designs to overcome these limitations, which could result in higher-capacity batteries for EVs.
Lithium-Sulfur and Lithium-Air Batteries
These next-gen battery chemistries promise higher energy densities than conventional lithium-ion batteries. Lithium-sulfur batteries, for instance, could reduce the weight of EV batteries, increasing vehicle efficiency and range. Lithium-air batteries, meanwhile, could theoretically match the energy density of gasoline, a breakthrough that would allow EVs to achieve ranges of 500 miles or more on a single charge.
Advancements in Battery Manufacturing and Recycling
As the demand for EV batteries grows, so does the need for sustainable and efficient manufacturing processes. Here are some ways companies are innovating in battery production and recycling:
Battery Recycling Technologies
Battery recycling is essential for the sustainable future of lithium batteries. New recycling methods, such as hydrometallurgical and direct recycling, are improving recovery rates for critical materials like lithium, cobalt, and nickel. Companies such as Redwood Materials and Li-Cycle are pioneering efforts to make battery recycling more efficient and environmentally friendly, aiming to minimize the carbon footprint of battery production.
AI and Machine Learning in Battery Design
Machine learning models can optimize battery chemistries and predict battery life cycles, accelerating the development of better batteries. This approach enables companies to test various materials and configurations without extensive physical testing, saving time and resources.
Modular Battery Manufacturing
The modular battery design allows manufacturers to create standardized battery modules that can be stacked together to meet different capacity requirements. This approach enhances flexibility, simplifies maintenance, and can reduce the cost of battery packs.
Challenges Facing the Future of Lithium Batteries in EVs
Despite these exciting advancements, lithium batteries face significant challenges:
Limited Supply of Raw Materials
The rising demand for lithium, nickel, and cobalt has led to supply chain issues and increased prices. This scarcity is driving innovation in alternative materials, such as sodium-ion batteries, but a sustainable solution is still necessary.
Environmental and Ethical Concerns
Mining for lithium and other raw materials has environmental and social impacts, including water depletion, habitat destruction, and labor rights issues. Sustainable sourcing practices and recycling technologies are essential to address these concerns.
Safety and Thermal Runaway Risks
Thermal runaway, where batteries overheat and catch fire, remains a concern, especially as batteries become more energy-dense. Technologies like solid-state batteries and improved battery management systems (BMS) are helping to mitigate this risk.
Future Outlook: The Role of Lithium Batteries in the EV Landscape
The EV industry is poised for rapid growth, with lithium batteries continuing to play a pivotal role. Here are some predictions for the future of lithium batteries in the EV industry:
- Greater Range and Faster Charging: The goal of achieving 500+ miles per charge with a 10-minute recharge time is within reach, especially with solid-state battery advancements.
- Lower Costs and Wider Accessibility: Battery prices are expected to decrease, making EVs more affordable and accessible to a broader range of consumers.
- Sustainable Manufacturing and Recycling Practices: As recycling technologies advance and circular economy principles gain traction, the environmental footprint of lithium batteries will shrink.
- Innovative Battery-as-a-Service (BaaS) Models: Battery swapping and leasing models are becoming popular, allowing EV owners to easily upgrade to better batteries without purchasing a new vehicle.
Conclusion
The future of lithium batteries is bright, with ongoing research and development promising to overcome current limitations and make EVs an even more attractive option. From solid-state technology to enhanced recycling, lithium batteries are driving the next wave of innovation in the EV industry, bringing us closer to a sustainable, zero-emission transportation future.
The lithium battery revolution is far from over, and as new breakthroughs unfold, the EV industry will continue to evolve toward a cleaner, more efficient, and accessible future for all.
References
- Gersdorf, T., Hensley, R., Hertzke, P., & Schaufuss, P. (2020). “The future of lithium-ion batteries and electric vehicles.”
McKinsey & Company.
Available at: McKinsey - BloombergNEF. (2022). “Battery Price Survey.”
Bloomberg New Energy Finance.
This annual report analyzes the price trends of lithium batteries and the cost trajectory.
Available at: BloombergNEF - Ziegler, M.S., & Trancik, J.E. (2021). “Re-examining rates of lithium-ion battery technology improvement and cost decline.”
Energy & Environmental Science.
Available at: Energy & Environmental Science - Vaalma, C., Buchholz, D., Weil, M., & Passerini, S. (2018). “A cost and resource analysis of sodium-ion batteries.”
Nature Reviews Materials, 3(4).
Available at: Nature Reviews Materials - Tarascon, J.M., & Armand, M. (2001). “Issues and challenges facing rechargeable lithium batteries.”
Nature, 414(6861), 359–367.
This seminal paper provides foundational knowledge on lithium battery technology and future challenges.
Available at: Nature - Wu, C., & Lai, J. (2022). “Recycling lithium-ion batteries from electric vehicles.”
Journal of Cleaner Production, 362.
Available at: Journal of Cleaner Production